
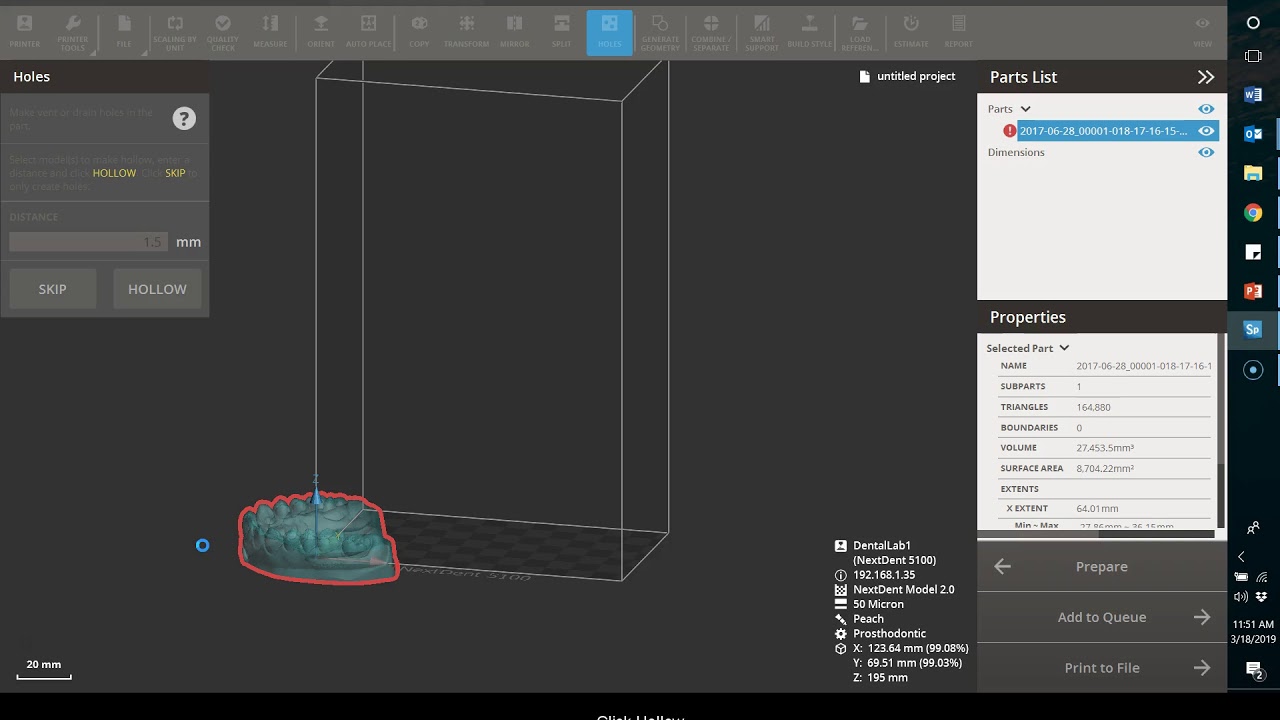
Sounds complicated, but it shouldn’t take more than a minute or two to make sure that it’s all good to go. To fix the holes, either step back to alias and make sure that there are no holes by remodeling the object, or:Įxport to STL anyways, and then re-import the STL back into Rhino, and run the command ‘_FillMeshHoles’. If it says “X surfaces or polysurfaces joined into one open polysurface.”, then your object has holes in it.
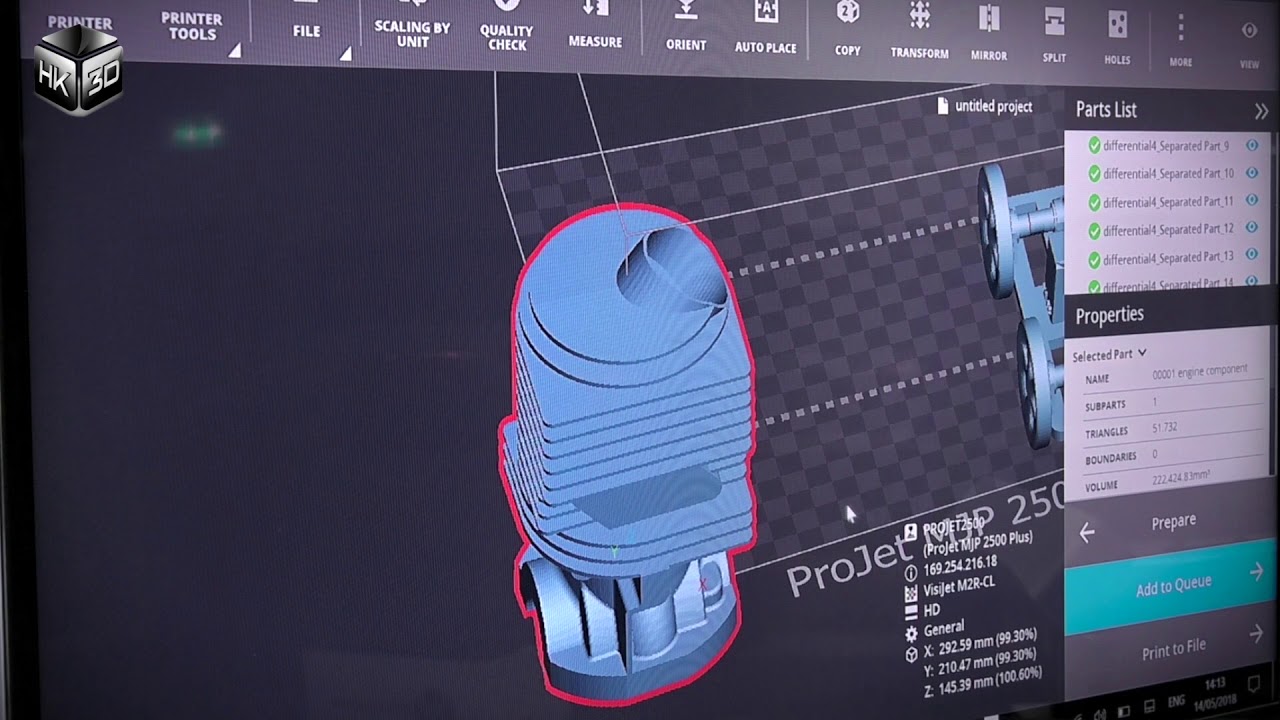
If that’s what you see, then you’re good to go for export to STL for printing. The output that you should see is “X surfaces or polysurfaces joined into one closed polysurface”.

Look in the command line at the top, and see what the command messages for the join command you ran are. Try reimporting the same IGES file into Rhino, and join all of the surfaces by selecting all of the surfaces (CTRL + A), and type ‘_Join’ and press Enter. Since you imported the model into rhino with IGES, it wouldn’t have imported with the surfaces joined…and then you exported those unjoined surfaces as an STL file, which resulted in X number of meshes being exported, X being the number of surfaces in the object. If parts come out weak, increase the saturation values by. This is the difference between a solid object and a polysurface. The ZPrint Software will recommend shell and core saturation values based on the part geometry. What this means is that even though you stitched your model in aliasstudio, it may have tiny naked edges, resulting in the volume of the object not being calculable. The issue is that your model isn’t ‘watertight’.
